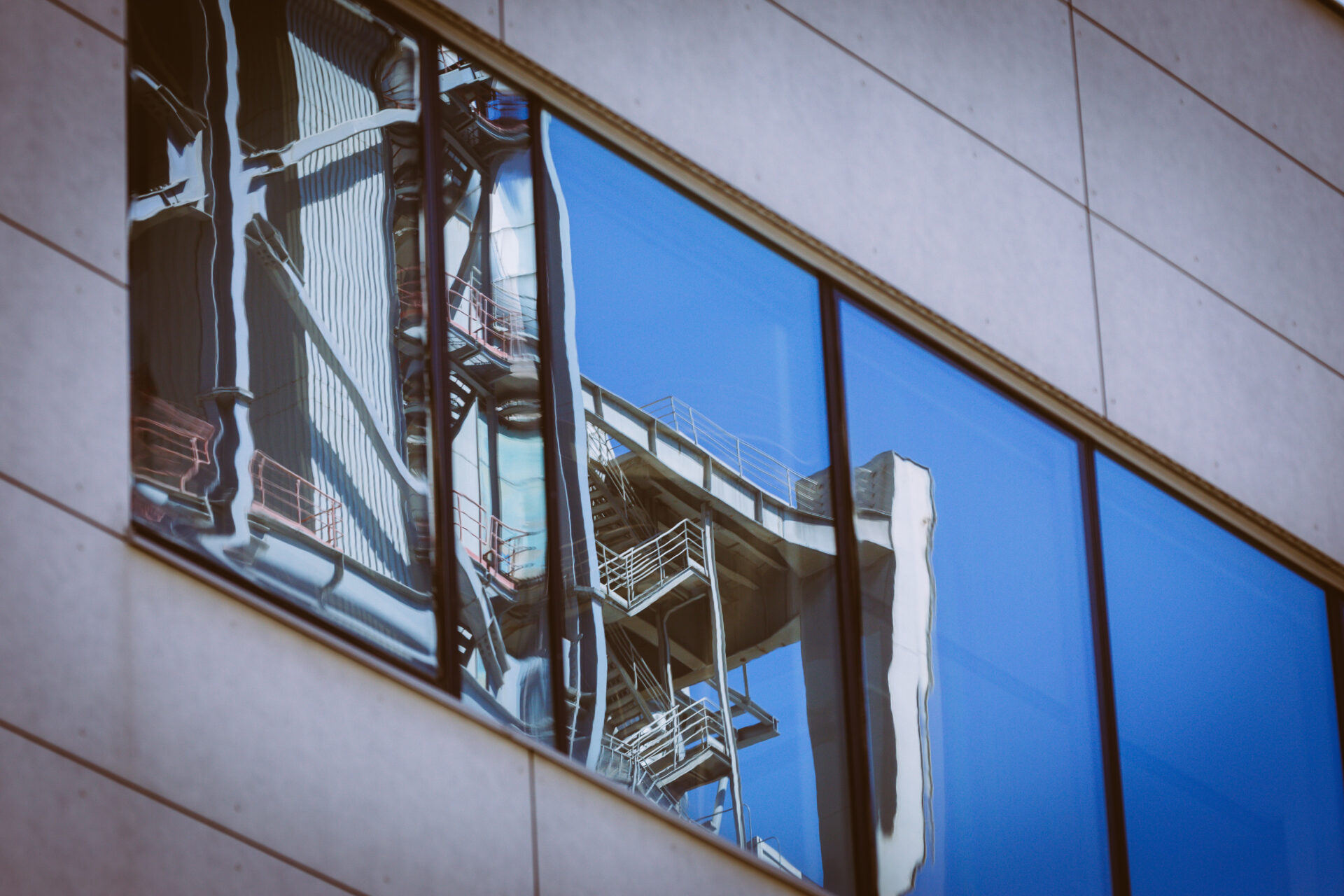
Tehnologija
V zadnjih 15-ih letih smo uspeli cementarno v Anhovem uvrstiti med najsodobnejše cementarne v Evropi. Ob tem ves čas spremljamo vplive na okolje in stanje okolja po lastnem načrtu, ki je bistveno obsežnejši od tistega, kar od nas zahteva zakonodaja. Z vrsto investicij ob nadaljnji uporabi energetsko bogatih odpadkov za gorivo bomo vplive še naprej zmanjševali.
Kamnolom
Osnovna surovina za proizvodnjo cementa je lapor, ki je homogena zmes apnenca in gline, nastala v preteklih geoloških dobah s sedimentacijo. Ker naravnega laporja ni več dovolj za masovno proizvodnjo, se surovinsko mešanico, ki mora vsebovati 75-78 % kalcijevega karbonata (CaCO3), pripravlja z mešanjem apnenih in glinenih komponent: od takih s 35 % CaCO3 do apnencev z nad 95 % CaCO3. Apnencu, ki je vir CaO, je običajno primešan dolomit, ki v sistem vnaša MgO. Glinene komponente so nosilci SiO2, Al2O3 in Fe2O3.
Osnovne surovine pridobivamo v kamnolomih Rodež in Perunk, ki se nahajata v neposredni bližini cementarne.
Črpanje poteka na dvanajstih etažah, kjer se surovine odstreljuje in odvaža na osnovno etažo v drobilnik.
Drobilnik
V fazo proizvodnje surovin uvrščamo tudi drobljenje. V drobilniku surovin se nasipani material drobi na granulacijo pod 30 mm, nakar se s tekočim trakom transportira v predhomogenizacijsko halo.
Predhomogenizacija
Ker se surovinsko mešanico pripravlja iz zelo različnih komponent, jih je treba dobro homogenizirati. Predhomogenizacija poteka tako, da se surovine po drobljenju s tekočimi trakovi transportira v predhomogenizacijsko halo na kup v približno 600 plasteh. Material, ki ga je na enem kupu okoli 23.000 ton, se odvzema prečno. Na ta način je dosežena dokaj dobra predhomogenizacija surovine. V predhomogenizacijski hali sta dva kupa, od katerih se eden uporablja za proizvodnjo klinkerja, drugi pa se pripravlja. Kup zadošča za enotedensko proizvodnjo. Nato gre material na tekočih trakovih preko presipne postaje v mlin surovin.
Vrečasti filtri
Vrečasti filtri služijo za odpraševanje vseh virov prašenja. V cementarni je postavljenih več kot 100 različnih vrečastih filtrov, linijo proizvodnje klinkerja (rotacijska peč, izmenjevalec toplote in oba mlina surovin) pa odprašujeta dva velika vrečasta filtra.
Mlina surovin
Predhomogenizirano surovinsko mešanico se transportira v dva mlina surovin, kjer se ta zmelje v laporno moko z dodatki:
– škaja in podobne železove komponente za korekcijo vsebnosti Fe2O3,
– kremenčev pesek, za korekcijo vsebnosti SiO2,
– apnenec za korakcijo CaCO3.
Nato gre laporna moka v homogenizacijska silosa, kjer poteka tudi zadnja faza homogenizacije.
Silosi laporne moke
Iz mlinov dobimo laporno moko, to je sivkast, fin prah, ki ga skladiščimo v dva homogenizacijska silosa, kapacitete 6.500 ton. Za polnjenje le-teh se uporabljajo elevatorji in zračne drče. Laporna moka gre nato skozi izmenjevalec toplote v peč.
Toplotni izmenjevalnik
Izmenjevalec toplote je prvi del v procesu pečenja klinkerja. Namen izmenjevalca je učinkovit prenos toplote iz dimnih plinov na laporno moko (ciklonski del) ter dekarbonatizacijo vseh karbonatov, predvsem kalcijevega v ustrezne okside (kalcinator s »hot diskom«). V »hot disk« doziramo odpadne gume, nad vstopom v peč, pod »hot diskom« pa zmlet premogov prah. Tako v toplotnem izmenjevalcu, kot v peči se dimni plini gibljejo protitočno glede na tok laporne moke. Pri tem prihaja do izmenjave toplotne energije med materialom in dimnimi plini. Ko dekarbonatizirana laporna moka pade v peč, ima temperaturo 880°C, dimni plini na tem mestu pa 1100°C. Dimni plini, ki zapuščajo izmenjevalec, imajo temperaturo 330-360°C. Izmenjevalec toplote je tudi dober filter za hlapne komponente (alkalije, žveplo, kloride, težke kovine), ki na ta način ostajajo v peči in ne zapuščajo sistema kot škodljive emisije.
Rotacijska peč
Laporna moka se skozi izmenjevalec toplote dozira v rotacijsko peč, ki ima obliko cevi premera 5 m in dolžine 68 m in se med obratovanjem vrti s hitrostjo 2,5 do 3,0 obrata/min. V peči se laporna moka pretvori v klinker. Potrebno energijo za pečenje klinkerja dovajamo z gorilnikom moči 100MW na izstopu klinkerja iz peči. Kot goriva uporabljamo zemeljski plin, zmlet petrol koks ter alternativna gorica. Klinker, ki izstopa ohladimo v rešetkastem hladilniku.
Silosi klinkerja
Klinker, ki izstopa iz hladilnika peči se skladišči v petih silosih skupne kapacitete 70.000 ton. Iz silosov se klinker transportira preko elevatorjev in ploščnih transporterjev do mlinov cementa.
Mlina cementa
Klinker se zmelje v komornih, krogličnih mlinih z različnimi dodatki v fin siv prah – cement. Glede na zahtevane lastnosti in predpisane standarde, lahko cementi vsebujejo sledeče dodatke:
– sadro – obvezen dodatek za regulacijo vezanja (v primeru pomanjkanja sulfata pride do prehitrega oz. lažnega vezanja),
– žlindre,
– pucolane (naravni in umetni),
– apnenec,
– elektrofilterski pepeli.
Zahtevane karakteristike za posamezne tipe cementa dosežemo z ustrezno finostjo mletja, pri tem so predvsem pomembni: specifična površina, ostanek na situ 90µm in ustrezna porazdelitev delcev ter z različnimi sestavami zgoraj naštetih dodatkov.
Silosi cementa
Cement se v skladišči v silosih cementa.
Odprema in transport cementa
Cement odpremljamo kamionsko in vagonsko – v razsutem stanju ali pakiranem v vreče.